Blog
Stud Welding Applications Guide
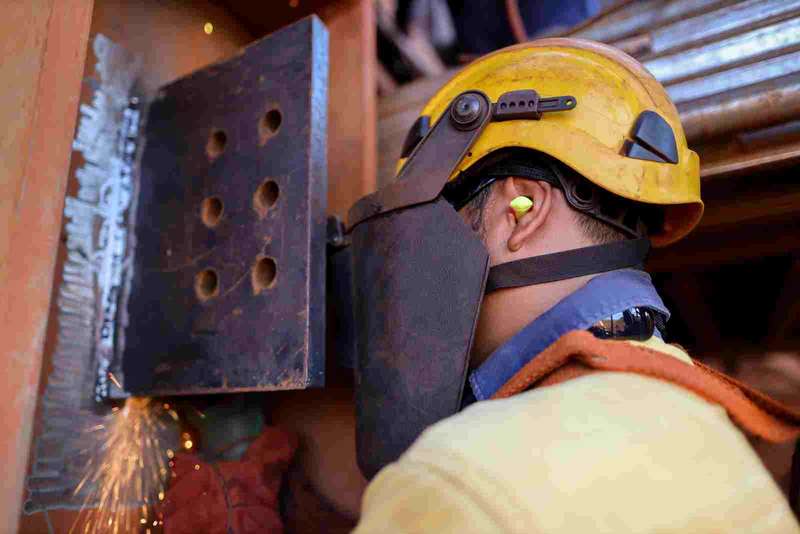
The Challenges of Traditional Fastening Methods
For decades, traditional fastening methods, such as bolting, riveting, and screwing, have been the cornerstone of construction, manufacturing, and assembly. However, these methods come with inherent challenges that can impact the efficiency, cost, and quality of projects as a whole.
Understanding each of these challenges is necessary for properly evaluating the advantages offered by alternative techniques like stud welding.
- Time and Labor Intensive: Traditional fastening methods often require multiple steps – drilling holes, aligning components, and then applying the fastener. This multi-step process demands significant time and labor, which can be especially cumbersome in large-scale or complex projects.
- Requirement for Dual-Side Access: Bolting and riveting typically require access to both sides of the joined materials. However, this dual-side access isn’t always feasible, especially in confined spaces or where one side of the assembly is inaccessible. This limitation can lead to significant design constraints and may necessitate the redesign of components or assemblies.
- Material Weakness: Drilling holes to insert bolts and rivets can significantly compromise the structural strength of the materials. Removing material to create a hole reduces the cross-sectional area, potentially leading to stress concentrations around the holes. This can be detrimental in applications where structural integrity and load-bearing capacity are important.
What Is Stud Welding?
Stud welding is a highly specialized form of welding that attaches a metal stud or similar fastener to a workpiece, usually another metal component, using a welding arc to create a permanent bond. This advanced welding technique finds extensive application in various industries, including automotive, construction, shipbuilding, and manufacturing, due to its efficiency and the strength of the resulting joint.
Stud welding is distinguished by its ability to form a high-quality weld quickly, often in a fraction of a second, and without the need for holes or additional preparation that traditional fastening methods require.
The Benefits of Stud Welding
One of the primary advantages of stud welding is its speed over more traditional fixing and fastening methods.
Traditional methods such as bolting or riveting require access to both sides of the workpiece and often involve multiple steps such as drilling, tapping, and then fastening. In contrast, stud welding is a single-step process that speeds up the manufacturing cycle while also reducing labor costs significantly.
Another significant benefit is the integrity of the joint that’s created by stud welding. Unlike bolts, which can loosen over time, or rivets, which may be prone to shearing under stress, the welded joint is permanent and less susceptible to failure under load or vibration.
This strength proves to be particularly beneficial in industries including the auto industry and shipbuilding, where the reliability and durability of every component are essential.
Real-World Stud Welding Applications
Stud welding, with its unique blend of speed, efficiency, and reliability, has found a prominent place in a variety of real-world applications. Across industries of all kinds, this technology revolutionizes how components are fastened and the way structures are built.
Industrial Fabrication
The industrial fabrication sector benefits significantly from stud welding, which provides the precision and strength needed for the mass production of a diverse range of products. This includes everything from the delicate components found in computer hardware to the robust assemblies required in industrial machinery.
Stud welding's capacity for providing precise and heavy-duty fasteners is invaluable for maintaining high production standards and efficiency in industrial manufacturing processes.
Learn more about Products We Provide For Industrial Fabrication here.
Compact Construction & Agriculture
When it comes to the compact construction and agriculture industries, stud welding supports the integrity and functionality of essential equipment. This technology is pivotal for attaching critical components, such as fuel tanks, to the cabs and chassis of compact construction machinery.
Large agricultural OEMs rely on the precision and durability of these fastening solutions to ensure their machinery can withstand the rigors of agricultural tasks and environments.
Learn more about Products We Provide For the Compact Construction & Agriculture industries here.
Civil Construction and Structural Steel Work
Stud welding is widely employed in the construction sector, especially in the assembly of steel and concrete structures. The technology allows for the fastening of steel beams, girders, and decking without the need to drill holes, preserving the integrity and strength of the steel.
Unthreaded Headed Anchor and Shear Connector weld studs are critical for securing poured concrete roadways and flooring to the steel structures supporting them.
Furthermore, stud welding is used for securing insulation and waterproofing materials to buildings, offering a clean and efficient method of attachment.
Stud welding also finds applications in public infrastructure projects, such as in the construction of tunnels, railway systems, and public transportation facilities.
In this category, it's used for attaching wear plates, cable management systems, and even signage. Its ability to create strong, vibration-resistant joints ensures long-term durability in these high-use public spaces.
Learn more about Products We Provide For the Civil Construction industry here.
Commercial Trucking and Transportation Industry
In the transportation sector, stud welding plays an important role in both manufacturing and repair procedures of on-road commercial trucks, trains, and buses. The method is ideal for attaching various components to vehicles' bodywork, chassis, and exhaust systems.
The ability to quickly and securely attach items without the need for drilling or additional preparation work is a boon to production lines, enhancing both speed and cost-effectiveness.
Additionally, in electric vehicle manufacturing, stud welding aids in the lightweight design of components, directly contributing to increased battery efficiency and vehicle range.
Learn more about Products We Provide For the Commercial Trucking and Transportation Industry here.
Shipbuilding
Stud welding is indispensable in shipbuilding, where it's used for attaching various components to the hull and decks, including insulation panels, electrical cable trays, and even decorative fixtures.
The robustness of stud welding ensures that these components can withstand the harsh marine environment characterized by constant moisture and salt exposure.
The technology's one-sided application capability makes it particularly well-suited for confined spaces found in ships, where traditional fastening methods would be impractical or impossible.
Learn more about Products We Provide For Shipbuilding here.
Electronics and Electrical Enclosures
Stud welding offers precision and reliability in the manufacture of enclosures for electrical distribution and electronic products.
It's also the best method to attach small metal parts to electronic assemblies where traditional welding would be too invasive or could potentially damage sensitive components. This proves to be essential in the production of household appliances, electronic gadgets, and components where precision and electrical conductivity are essential.
Learn more about Products We Provide For the Electric Power Industry here.
Hydraulic Cylinder Manufacturing
Cylinder manufacturing is a process that benefits from the precision and reliability of stud welding. An automated stud welding station allows hydraulic ports to be welded onto a cylinder in a fraction of the time that conventional MIG welding requires, with 100% of the port base welded and without any distortion to the cylinder.
Stud welding equipment and accessories supplied by Image Industries ensure that these components are attached with the exact specifications required for optimal performance and reliability in various applications.
Learn more about Products We Provide For Cylinder Manufacturing here.
Food Service
In the food service industry, the quality and cleanliness of metal components are essential to ensuring strict food safety standards are upheld. Stud welding plays a key role in the prototyping and production of these components, ensuring they are free from imperfections such as grooves, pits, and pinholes that could harbor bacteria.
This is especially important for components used in food production and packaging, where corrosion resistance and the ability to withstand rigorous cleaning processes are critical for maintaining health and safety standards.
Learn more about Products We Provide For the Food Service industry here.
Nuclear
The nuclear industry demands the highest standards of quality and precision in welding, given the critical importance of safety and durability in nuclear power plant construction. Stud welding, with its ability to provide strong, reliable fastenings, is an essential part of the construction and maintenance of these facilities.
Products used in this sector must meet stringent requirements for chemical composition, product cleanliness, strength, and corrosion resistance to ensure the long-term safety and integrity of nuclear installations.
Learn more about Products We Provide For the Nuclear iIndustry here.
Trust the Stud Welding Experts
By now, it's pretty clear that stud welding is more than just a method; it's essential when it comes to manufacturing and construction. Its unique blend of speed, durability, and precision opens up a new world of possibilities and potential for sectors of all kinds spanning from automotive to shipbuilding.
To further explore stud welding, Image Industries Inc. stands out as the go-to resource to help. With their extensive array of weld studs, cutting-edge stud welding equipment, and versatile stud welding accessories, they’re much more than just suppliers; they’re partners in your journey towards more efficient and robust manufacturing solutions.
Building lasting bonds since 1976.
Providing superior stud welding and stud welder parts and equipment isn't enough. We also strive to deliver better service and unmatched expertise. And that's exactly what we've been doing for more than 40 years.
Read About Our History