Blog
Solutions to Common Challenges Faced in Stud Welding
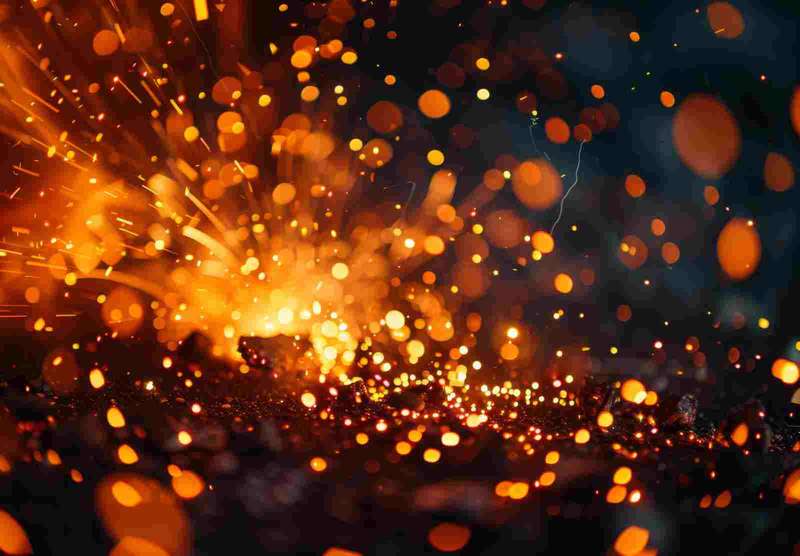
Stud welding is an important process used in a variety of industries and is known for its strength and reliability in joining different components together. However, as with any manufacturing technique, it presents a range of challenges that professionals must be able to understand and overcome to deliver the best results in their work.
Understanding each of these common issues, from equipment malfunctions to material compatibility, is essential for maintaining the integrity of your stud welding process over time.
General Challenges in Stud Welding
Stud welding, like any welding process, comes with a set of challenges that can affect the quality and durability of the welds. Some of the more common issues result from incorrect settings or techniques, leading to inconsistent or less than optimal welds.
Equipment failures, such as malfunctioning welding guns or power sources, can also disrupt the welding process and result in subpar welds. Material incompatibility also poses significant challenges; welding dissimilar metals or using unsuitable materials can lead to poor fusion and weakened structures.
Early identification and resolution of these challenges are absolutely essential. Conducting quality assurance before beginning the weld—by making sure that all equipment is functioning correctly, materials are compatible, and the appropriate technique is used—can prevent defects and minimize the need for rework, ultimately saving time and costs.
Drawn Arc Stud Welding Challenges
Drawn Arc stud welding is a process in which an electric arc is used to melt the bottom of a weld stud and the metal surface beneath it, forming a pool of molten metal for less than a second that then solidifies into a strong connection.
While this method is effective, it can present certain stud welding challenges that can impact the quality and reliability of your welds.
Arc Blow
Arc blow is a problem that happens when the welding arc, the electrical current used in welding, becomes unsteady and moves in an unwanted direction. This can happen because of magnetic forces or if the grounding clamp is not set up correctly. When the arc is skewed due to improper grounding techniques, it can cause the weld to be less than optimal.
To reduce the chances of arc blow, you can adjust the location of the grounding clamp on the metal you’re working on. This helps control the magnetic forces and keeps the weld steady.
Weld Quality Consistency
Inconsistent weld quality in Drawn Arc and CD stud welding can result from fluctuations in power supply and operator errors.
To maintain consistent welds, it's important to regularly check the plunge and lift settings of your weld tools (weld guns) so they operate within the recommended parameters. You also want to check that operators are properly trained to help reduce errors and improve their technique.
Monitoring power supply stability and using reliable equipment can also help you achieve more consistent weld quality over time.
Material Compatibility
The stud welding process is most effective when the weld stud and the metal surface are made from similar metals, and when those metals have some electrical and thermal resistance.
For the best stud welds, choose materials that work well with Drawn Arc and CD stud welding, such as low-carbon steels, stainless steels, aluminum, Inconel, and Monel, and ensure they are properly prepared before welding.
Capacitor Discharge (CD) Welding Challenges
Capacitor Discharge or CD welding is a fast welding method that uses a burst of electricity from a capacitor to attach studs to a base material. It’s popular because of its speed and accuracy, with minimal heat impact, which helps prevent warping or distortion of the material.
CD welding is especially useful for thin materials and situations where appearance and precision matter, though it does come with its own set of challenges.
Ignition Tip Height
Ignition Tip Length: The length of the ignition tip is crucial for weld quality. A shorter tip reduces the weld time, which can result in insufficient metal melting and incomplete fusion.
- Positioning Issues: Using center punch marks for stud placement can create small dips in the metal, causing the ignition tip to sit lower and shorten the arc time, which compromises weld quality. To avoid this, use precise fixtures or guides for accurate stud positioning instead of relying on center punch marks.
Surface Preparation
Smooth, clean surfaces are essential for quality results when welding. The rapid welding process means that any surface roughness or contamination, such as rust, oil, or paint, can prevent proper metal melting and lead to weld failures.
Making sure that working surfaces are well-prepared and free of contaminants is essential for achieving high-quality welds, every time, for both Drawn Arc stud welding and CD stud welding.
Material Penetration
CD welding can be challenging with medium- and high-carbon steels, as well as hard or high-tensile materials, because the short arc time makes it difficult to penetrate these tougher metals effectively.
Additionally, both CD stud welding and Drawn Arc stud welding are ineffective with steels or stainless steels that have a carbon content above 0.2%.
Plating and Painting Compatibility
Both Drawn Arc and CD stud welding are best performed using weld studs that are not plated (bare) on the welded end and with a mating substrate that is likewise unplated. The only exception to this is to plate a copper “flash” of less than 5 micron thickness to CD weld studs made from low-carbon steel to improve their welding conductivity.
Note that stud welding either zinc-plated weld studs or zinc-plated steel substrates is generally not recommended because the heat of the welding process creates zinc oxide. The resulting reaction can lead to poor weld quality and even potential health risks.
Common Solutions and Best Practices
For welds to meet the highest standards of quality, you must maintain your stud welding equipment and make sure that it’s clean. By consistently maintaining and inspecting your stud welding tools, you can avoid the common pitfalls of contamination and guarantee that they operate at their optimal efficiency.
The proper setup of your welding equipment is also important here, and this includes checking settings and calibrations before starting a job. Holding regular, ongoing training for operators helps them stay updated on best practices and techniques to help further reduce errors.
Reviewing the appropriate operation manuals is the only way to fully understand how to set up, calibrate and maintain your respective piece of welding equipment, such as power supplies and weld tools/guns.
To address the distinct challenges in Drawn Arc and CD welding, try to use precise fixtures or guides for accurate stud placement and choose appropriate materials to avoid compatibility issues. For both forms of stud welding, make sure surfaces are smooth and clean, and avoid zinc-plated materials.
The importance of regular equipment maintenance and calibration cannot be overstated, as these practices prevent malfunctions and help maintain consistent weld quality. Through periodic checks and servicing, you can help make sure that your equipment remains in optimal condition to deliver dependable performance, every time.
Image Industries’ Selection of Stud Welding Supplies
Overcoming the common challenges in both Drawn Arc and CD stud welding requires a deep understanding of the techniques involved and close attention to detail when working. Through understanding, recognizing, and addressing the potential challenges associated with each type, welders can significantly improve the outcome of their work.
For those trying to overcome these challenges with precision and expertise, Image Industries Inc. offers a wide selection of weld studs, stud welding fastening systems, and stud welding accessories. Visit us online to find the parts you need or reach out for a quote today for more information.
Building lasting bonds since 1976.
Providing superior stud welding and stud welder parts and equipment isn't enough. We also strive to deliver better service and unmatched expertise. And that's exactly what we've been doing for more than 40 years.
Read About Our History