Blog
Repairing vs. Replacing Stud Welding Equipment
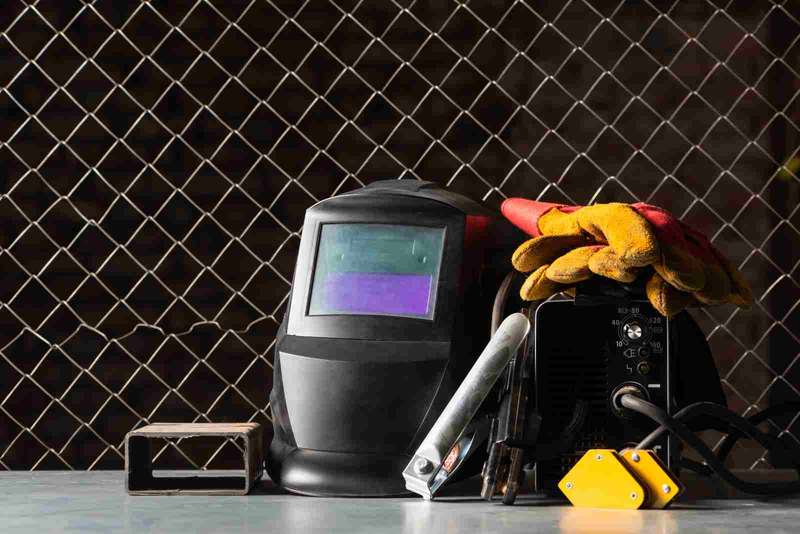
Deciding whether it’s time to repair or replace your stud welding equipment can be challenging, especially as wear and tear become unavoidable. Even the best equipment eventually shows signs of age.
Understanding when it's time to invest in new equipment versus making repairs is essential for maintaining both productivity and safety in your fabrication processes. Equipment reliability directly impacts your ability to meet production goals, making it vital to evaluate your options carefully and make the right choice for your needs.
The Evolution of Stud Welding Equipment
Stud welding has been a fundamental fabrication process since the early 1900s, and during that time, the equipment has seen continuous advancements in terms of design, efficiency, and ergonomics. Early models were purely mechanical and lacked the precision that modern welding demands.
Although equipment hasn’t changed much in the last 15 years, compared to decades ago, current stud welding equipment represents a significant leap forward, offering greater control over weld parameters, improved reliability, and enhanced safety features. These advancements have made stud welding more efficient and far more adaptable to the needs of contemporary fabrication shops.
When Repairing is a Viable Option
Minor issues of wear and tear can often be addressed through simple repairs, helping extend the life of your stud welding equipment without requiring any major investments.
Regular maintenance, when affordable, often makes more financial sense than jumping straight to replacement. Taking this approach allows you to get the most out of your equipment while keeping your operational costs in check.
However, repairs should only be considered if the equipment does not pose a safety hazard—such as dangerous shocks or brittle wiring—since safety must always come first in your decision-making process.
Signs That Replacement is Necessary
Unfortunately, obsolescence can make replacement the only practical option to go with especially when your equipment is over 15 years old. When parts for your stud welding equipment become difficult or impossible to find, it often means the machine is outdated, and repairs will only lead to diminishing returns.
High repair costs and frequent breakdowns are other important indicators that you may have to invest in a new system. For instance, worn wiring or disintegrating cable connections can lead to constant downtime, negatively impacting your productivity.
Older equipment also poses increased safety hazards for your work environment. Frequent shocks, for example, signal that the system may be unsafe, putting both weld quality and operator safety at risk. Investing in new equipment at this stage protects both your workers and the quality of your projects, making it a worthwhile decision.
Challenges with Older Equipment
Older stud welding equipment can be bulky and inconvenient, making it difficult to move around the workshop and reducing overall efficiency. If you have equipment older than 15 or 20 years, then upgrading to new equipment provides significant benefits, saving time and effort while allowing your team to work far more effectively.
Alongside this, maintenance is another challenge that’s posed by utilizing outdated equipment. The overhead costs of keeping old machines running may not seem like a major issue until a sudden breakdown occurs, leading to costly, unexpected downtime and disrupting your workflow. Investing in newer equipment reduces these often poorly timed costs, offering a more stable and efficient operation over the long term.
The Impact of Low Productivity
Frequent breakdowns of your welding machines can severely impact your organization’s productivity and make it far more challenging to hit output targets. If your stud welding machine breaks down multiple times in just a few months, it doesn’t just interrupt your workflow—it also leads to frustration and costly delays.
The opportunity cost of downtime adds up quickly—time that’s spent on repairs could be used to complete projects and meet those important client deadlines. Replacing any unreliable equipment can help you avoid these setbacks, allowing you to maintain steady productivity and focus on achieving your goals without constant disruptions.
Weighing Essential Factors to Drive Your Decision
When deciding whether to repair or replace your stud welding equipment, consider the main factors: the cost of ongoing repairs compared to replacement, safety concerns, and potential improvements in efficiency.
While repairs may seem like the cheaper option at first, taking a long-term view often reveals that investing in new equipment brings sustainable benefits. New machines often end up saving you time and money in the future.
Repair or Replace: The Choice Is Yours
An assessment of your welding equipment's condition, repair costs, and safety issues is essential to making the right decision between repairing and replacing. Regular evaluations help you maintain the right balance, keeping your operation safe, productive, and cost-effective.
If you’re considering repairing your equipment or investing in something new, take a look at what Image Industries has to offer your organization. From expert repair services to the finest selection of stud welding equipment and accessories, our goal is to support your needs.
Building lasting bonds since 1976.
Providing superior stud welding and stud welder parts and equipment isn't enough. We also strive to deliver better service and unmatched expertise. And that's exactly what we've been doing for more than 40 years.
Read About Our History