Blog
A Stud Welding Terminology Refresher
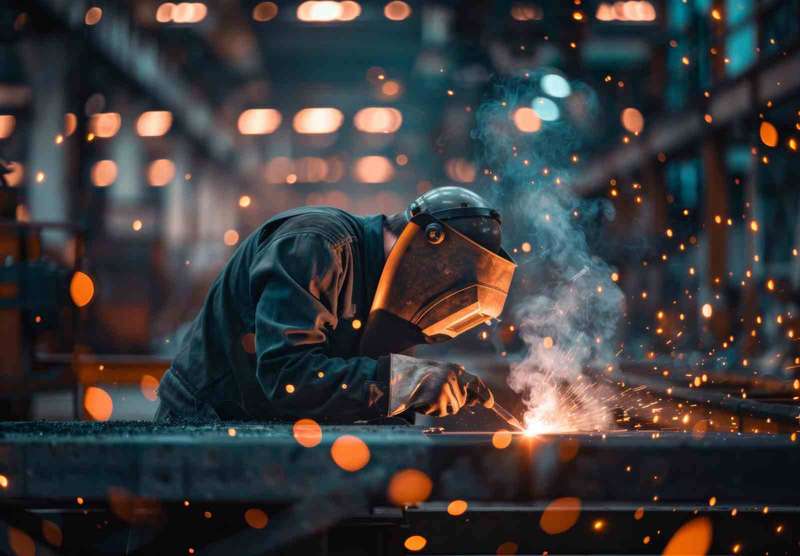
Stud welding is a precise and essential process that’s widely used across a spectrum of industries, but its specialized terminology can sometimes be tricky to keep straight.
To help you stay on top of your game, this refresher will walk through the primary terms and concepts that are involved.
Essential Equipment for Stud Welding
Two important elements in the stud welding process are the weld studs and ceramic ferrules, each playing a distinct role in creating a successful weld.
Weld Stud
Weld studs are metal fasteners, either cold-formed or CNC machined, designed to be welded onto similar metals, and they come in two types: threaded and unthreaded.
Threaded weld studs serve as fasteners, while unthreaded studs function as pins or locators, helping with positioning or attachment in various applications.
Ferrule
Ceramic ferrules act as essential protective barriers during the Drawn Arc stud welding process. Positioned around the stud, they contain the molten metal and prevent it from splashing, helping to maintain the cleanliness and integrity of the weld zone.
Ceramic ferrules withstand the high temperatures involved to maintain a controlled and efficient welding environment.
Primary Parts of the Stud Welding System
Each piece of equipment in a stud welding system plays a specific role, from supplying power to holding and transporting the weld studs, which work together to make sure the process runs efficiently.
Power Source
The welding process is initiated and completed thanks to the energy supplied by the power source. Stud welding systems typically use one of three types of power sources: Arc, QuickLinx, or Capacitor Discharge.
Arc welding offers the strongest bonds, QuickLinx is designed for faster setups, and Capacitor Discharge focuses on precision with smaller fasteners and cleaner welds.
Weld Tool/Gun
The weld tool, often called a weld gun, is responsible for holding the studs and delivering the necessary heat to fuse them with the base material.
These tools can be handheld for portability and flexibility or fixed in automated systems for high-volume, consistent production.
Ground Cable
The ground cable is essential when it comes to maintaining safety during the welding process and provides a safe path for excess electrical currents.
Extension Cable
An extension cable connects the power source to the weld gun, carrying the necessary current to the tool. It is critical for maintaining consistent energy flow during the weld.
Different Methods for Stud Welding
Having a solid foundational understanding of each of the different stud welding methods helps in selecting the right process for achieving optimal results, from strong structural bonds to precise, clean finishes.
Drawn Arc Welding
Drawn arc welding creates the strongest bond between the stud and the base material and is ideal for heavy-duty applications requiring durability.
The process uses a flux embedded in the stud to maintain a clean weld zone, while a ceramic ferrule surrounds the molten metal to prevent splashing and help shape the weld fillet.
Gas Drawn Arc Welding
Gas drawn arc welding substitutes the ceramic ferrule with a shielding gas to protect the weld area. This method facilitates a greater degree of automation while also sacrificing some control over the molten puddle, which may affect weld depth and consistency.
Short Arc Welding
Short arc welding doesn’t use a ferrule or flux like gas drawn arc welding; instead, it accelerates the process by using high currents and short weld times. While this increases speed, it introduces risks like porosity and reduced bond strength, making it suitable only for specific applications.
Capacitor Discharge Welding
Capacitor discharge or CD welding is used for smaller fasteners, providing a rapid and precise weld with minimal heat impact.
Contact CD Welding
During contact CD welding, the stud is placed onto the workpiece, and the discharge of current vaporizes the stud's tip. This creates an arc between the stud and the workpiece, melting the metal and allowing the stud to be plunged into the molten weld pool.
Gap CD Welding
In Gap CD welding, the stud is lifted to create a small gap between it and the workpiece before the welding process begins. As voltage is applied, the stud is released and accelerates across the gap to create a rapid and precise weld. This process is optimal for stud welding highly conductive metals, including aluminum.
Common Stud Welding Terms
- Amperage: Amperage refers to the electrical current flowing during the weld. It directly impacts the heat generated, which is important for forming a proper weld.
- Arc-Blow: Arc-blow occurs when the weld fillet is repelled away from the ground connection due to electric fields generated during welding.
- Bellows: Bellows are rubber boots that slide over the chuck adapter to keep dirt, weld spatter, and other contaminants from entering the internal mechanism of the weld tool.
- Burn Off: Burn off describes the portion of the stud consumed during welding. It contributes to the weld fillet being formed, affecting the strength and integrity of the bond.
- Burn Through: Burn through happens when the weld distorts or melts through the base material, often due to excessive heat or using material that is too thin.
- Chuck: Holding the weld stud in place during welding, the chuck is a consumable component that requires replacement when it becomes worn.
- Chuck Adapter: The chuck adapter attaches the chuck to the internal lifting mechanisms and transfers the weld current from the cable to the chuck, ultimately delivering it to the stud.
- Control Cable: The control cable serves as the connection between the stud weld tool and the controller.
- Controller: It’s the controller that starts the pilot arc, sends the lift signal, begins the weld current at the right time, and regulates the weld duration. Controllers can be external units or integrated within self-contained systems.
- Current: Current refers to the flow of electricity, expressed in amperes (Amps). Stud welding uses direct current (DC), which flows in one direction. The amount of current needed specifies the appropriate welding cable size.
- Ferrule Grip: The ferrule grip holds the ferrule in place throughout the weld process. Like the chuck, its consumable and needs to be replaced when it’s worn.
- Fillet: The fillet, a ring of weld metal around the stud post-welding, plays a key role in strengthening the weld.
- Flux Ball: The end of most weld studs contains a flux ball, which is pressed into place. It vaporizes during the weld, consuming oxygen at the weld site and reducing contamination.
- Foot: As part of the stud welding tool, the foot is connected to the legs, securing the ferrule grip and determining the plunge depth.
- Ground: Grounding the equipment allows for safe operation, directing any leaked voltage away from the operator. Proper grounding prevents electrical shorts and protects the user.
- Hang Up: A hang-up happens when the stud does not plunge into the weld pool correctly, often due to misalignment with the ferrule or internal mechanism issues. Adjusting the foot can fix this issue.
- Lift: Lift is the upward motion that creates a gap between the stud and base material, allowing the welding current to generate heat.
- Pilot Arc: The pilot arc is the initial arc formed when the stud is lifted from the workpiece.
- Plunge: Plunge refers to the portion of the stud, usually around 1/8 inch, that protrudes beyond the ferrule when the tool is at rest.
- Plunge Damper: The plunge damper reduces the rate at which the stud enters the weld pool, minimizing splatter and forming a uniform fillet.
- Resistance: Resistance measures how much current flow is opposed by materials, expressed in Ohms. Resistance generates heat, which is crucial for stud welding. Cable length and diameter affect resistance levels.
- Spark Shield: The spark shield is used in the foot of the weld tool to protect the operator from welding sparks. It also ports gas in gas welding applications.
- Time: Weld time is the total duration of the weld itself.
- Voltage: The potential power difference between two points is called voltage. In stud welding, DC voltage is applied to create the needed current flow, and higher voltages lead to stronger welds.
Learn At Any Stage From The Stud Welding Experts
For additional resources, expert advice, and high-quality stud welding equipment and accessories, contact Image Industries.
Image Industries is available to provide the tools, accessories, and information you need to stay informed and prepared. Contact us today for additional information or to request a quote on our products or services.
Building lasting bonds since 1976.
Providing superior stud welding and stud welder parts and equipment isn't enough. We also strive to deliver better service and unmatched expertise. And that's exactly what we've been doing for more than 40 years.
Read About Our History